Реферат: Монтажная микросварка
Реферат: Монтажная микросварка
Министерство
образования Республики Беларусь
Учреждение
образования «Белорусский государственный университет информатики и
радиоэлектроники»
кафедра
РЭС
РЕФЕРАТ
На
тему:
«МОНТАЖНАЯ
МИКРОСВАРКА»
МИНСК,
2008
Монтажная микросварка
применяется при монтаже кристаллов ИМС с помощью золотых и алюминиевых выводов.
Процесс УЗ-микросварки основывается на введении механических колебаний УЗ-частоты
в зону соединения, что приводит к пластической деформации приконтактной зоны,
разрушению и удалению поверхностных пленок с созданием атомно-чистых
(ювенильных) поверхностей, что интенсифицирует процесс образования активных
центров и тем самым приводит к образованию прочного сварного соединения без
большой пластической деформации свариваемых деталей.
Наиболее часто применяются
продольные колебания частотой 66 кГц , вводимые в зону сварки с помощью
волноводной системы (рис. 1.), состоящей из преобразователя 1,
акустического трансформатора 2, концентратора 3. Колебания от
рабочего инструмента 4 сообщаются проволочному выводу 5,
совмещенному с контактной площадкой 6, расположенном на акустической
опоре 7. Волноводная система крепится в узле колебаний держателем 8.
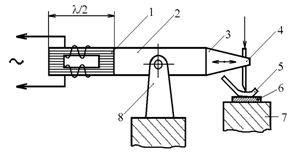
рис. 1. Схема ультразвуковой микросварки
Режим сварки на заданной частоте
характеризуется следующими параметрами:
1) энергией ультразвуковых
колебаний Е:
,
где A - амплитуда колебаний ( 2-5 мкм); F - частота
колебаний; t - время микросварки. Увеличение времени сварки повышает
прочность сварного соединения за счет роста суммарной площади очагов
схватывания до определенного предела, увеличение времени более 3-5с приводит к
усталостному разрушению соединения;
2) акустической мощностью Рак,
вводимой в сварочную зону, которая связана с электрической мощностью Р,
подводимой к преобразователю, соотношением
,
где hм - механический КПД преобразователя (0,5-0,7 для
магнитострикционных, 0,8-0,9 для пьезоэлектрических); Р0 - мощность
потерь на подмагничивание;
3) контактным усилием сжатия F,
которое зависит от толщины свариваемых элементов и подводимой мощности. При
недостаточном усилии сжатия не достигается необходимое сцепление между
инструментом и деталью, так как происходит проскальзывание инструмента по
детали. Увеличение усилия сжатия приводит к чрезмерной деформации сварной точки
и снижению прочности соединения. Оптимальная степень обжатия вывода выбирается
в соответствии с коэффициентом деформации 0,5-0,6:
,
где dпр - диаметр
проводника; Нд - высота деформированной зоны;
4) формой рабочей части
инструмента, которая выбирается из соображения, что длина деформируемого при сварке
проводника должна быть равной 2-3 диаметрам проводника. Повышению прочности
способствует небольшой паз в центре рабочей части вдоль свариваемой проволоки.
Функциональные особенности
конструктивных элементов инструмента при УЗ-микросварке заключаются в следующем
(рис. 2.):
·
диаметр направляющего отверстия выбирается из условия устранения
возможности забивки его материалом привариваемой проволоки:
;
·
угол наклона направляющего отверстия определяется условиями
перемещения инструмента на вторую сварку, зависит от высоты и длины проволочной
перемычки:
,
где h - высота
проволочной петли; g - перемещение
стола. Оптимальная величина угла a
составляет 30°;
·
длина рабочей части инструмента L определяет длину
деформируемой при сварке проволоки и выбирается из соотношения ; оптимальное значение L
составляет 0,1 мм для проволоки диаметром 27 мкм и 0,2 мм для проволоки
диаметром 60 мкм;
·
глубина продольного паза b зависит от коэффициента деформации
kд = 0,6:
b = (0,01 - 0,05) мм;
·
удаление выхода отверстия от задней кромки рабочей площади
инструмента должно обеспечивать симметрию петли проволочной перемычки: lуд
= 8 dпр;
·
угол наклона задней кромки рабочей площадки b должен обеспечивать подрезку проволоки
после второй сварки без остаточных напряжений в ней. Оптимальная величина угла b составляет 60°.
·
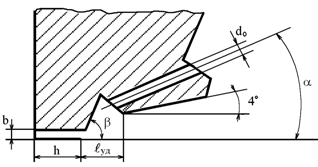
рис. 2. Рабочая часть инструмента для УЗ-микросварки
Для присоединения внахлест
проволоки из алюминиевых сплавов УЗ-микросваркой используют капилляры из
твердых сплавов типа ВК-20 с упрочненной рабочей поверхностью типа КУТ32 - 27 -
95 - 15, где КУТ - капилляр для УЗ - и термозвуковой сварки, 27 - диаметр
проволоки, 95 - размер L, 15 - размер R.
Анализ факторов, влияющих на
качество и надежность микросварных соединений, показывает, что все
технологические параметры УЗ-микросварки оказываются настолько тесно
связанными, что неудачный выбор одного из них изменяет ранее установленные
значения других. Поэтому для обеспечения высокого качества и воспроизводимости
ультразвуковой сварки важны: обеспечение заданной микрогеометрии поверхности
контактных площадок; оптимизация технологических параметров УЗ-микросварки
методом математического моделирования; разработка новых способов микросварки с
активацией процесса физико-химического взаимодействия контактирующих металлов.
УЗ-микросварка позволяет соединять без значительного нагрева самые
разнообразные металлы (алюминий, медь, никель, золото, серебро), а также
металлы с полупроводниковыми материалами. Выполнение проволочного соединения
контактной площадки на кристалле с траверсой корпуса требует наряду со
сварочными операциями действий по совмещению инструмента с местом сварки на
кристалле и корпусе схемы.
В 80-х гг. создана полностью
автоматизированная установка УЗ-микросварки ЭМ-4020, имеющая управляющую
микроЭВМ "Электроника-60",что резко увеличило производительность до
12500 сварок в час. Новое поколение установок, к которому относится ЭМ-4060,
построено с применением линейных шаговых двигателей и системы технического
зрения, что обеспечивает наивысшую производительность от 18 до 30 тыс. сварок в
час (табл. 1).
Табл. 1 - Характеристика
установок УЗ-микросварки
Параметры |
ЭМ-4020б |
ЭМ-4060 |
Мод. 1484 (США) |
Производительность, сварок/ч |
14 000 |
16 000 |
18 000 |
Диаметр проволоки, мкм
|
27-60 |
25-40 |
20-60 |
Размеры рабочего поля стола, мм |
25´25 |
30´30 |
101´51 |
Точность позиционирования, мкм |
25 |
20 |
3,2 |
Усилие сжатия, Н |
0,2-1,2 |
0,2-1,2 |
0,2-0,25 |
Тип сварочного соединения |
Внахлестку |
Встык-внахлестку |
Термозвук, золотым шариком |
В
новых моделях автоматов (ЭМ-4060П и ЭМ-4020П) для присоединения выводов ИМС
используется единая стойка управления, состоящая из однотипных блоков
управления, распознавания и питания ультразвуковых генераторов (УЗГ), а также
прецизионные загрузочно-разгрузочные устройства (ЗРУ) и оптико-телевизионные
системы.
Система
технического зрения (СТЗ) позволяет распознавать и определять положение
кристаллов и траверс. Положение корпуса определяется по одной траверсе при
совмещении только по линейным координатам и по двум траверсам при совмещении по
линейным координатам и углу. СТЗ может определять положение каждой траверсы
индивидуально.
Усовершенствованная
УЗ-система автоматов характеризуется следующими особенностями. Предусмотрена
непрерывная автоматическая подстройка частоты (АПЧ) в полосе не менее 5 кГц с
погрешностью отслеживания частоты резонанса ультразвукового преобразователя
(УЗП) не более 20 Гц и времени захвата не более 20 мс. Встроенная
модернизированная система контроля функционирования и компенсации ошибок АПЧ
позволяет вдвое (по сравнению с ЭМ-4020б) уменьшить максимальную длительность
компенсации ошибок АПЧ (время модуляции), увеличить устойчивость АПЧ и
обеспечить заблаговременную сигнализацию об отказе системы.
В
УЗ-системе имеется датчик, сигнализирующий о создании требуемого акустического
контакта между инструментом и соединяемыми деталями и позволяющий не только
определять позицию сварки по координате Z, но и увеличивать
воспроизводимость качества соединений. Подача УЗ-колебаний на инструмент
(дежурного сигнала) в промежутках между сварками снижает трение между
инструментом и проволокой при формировании петли, облегчает отделение
инструмента от сформированного соединения. Встроенное устройство контроля
сварочных систем, программно и аппаратно поддержанное управляющей системой установки,
позволяет осуществлять функциональное диагностирование УЗ-системы и непрерывное
наблюдение за ходом процесса формирования каждого сварного соединения и на этой
основе осуществлять 100%-й контроль качества при сборке ИМС любого типа в любом
корпусе.
Для
повышения качества и надежности микросварных соединений применяют различные
методы активации: электрическим током и ИК-излучением. Импульс электрического
тока пропускают через оба соединяемых элемента в направлении, обеспечивающем
электроперенос диффузионно-подвижного металла в соединении (рис. 3, а).
Поскольку в соединении Al-Ni алюминий обладает большим коэффициентом диффузии,
чем никель, электрический ток через соединение стимулирует диффузионное
взаимодействие в процессе микросварки, что приводит к образованию
интерметаллидов Al3Ni, имеющих повышенную прочность, и вызывает
увеличение надежности микросварного соединения.
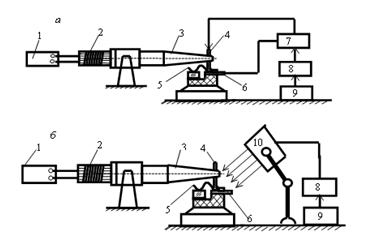
рис. 3. Схемы
УЗ-микросварки с токовой активацией (а) и ИК-активацией (б): 1 - генератор УЗ-колебаний; 2 -
преобразователь; 3 - волновод; 4 - инструмент; 5 -
проволока; 6 - контактная площадка; 7 -
устройство токовой активации; 8 - блок питания; 9 - блок
управления; 10 - блок ИК-активации
ИК-подогрев
соединяемых элементов при УЗ-микросварке снижает до минимума эффект
проскальзывания проволочного вывода, увеличивает его пластичность, степень
деформации и фактическую площадь контакта вывода с контактной площадкой (рис. 3,
б). Кроме того, тепловая активация соединения до температур, не
превышающих температуру рекристаллизации металлов, участвующих в соединении,
ускоряет диффузионные процессы в зоне контакта, что в итоге способствует
увеличению прочности микросварных соединений и повышению надежности изделий.
Термозвуковая
сварка (ТЗС) находит все возрастающее
применение при сборке изделий микроэлектроники. В ТЗС соединения формируются в
результате совместного действия температуры, энергии ультразвуковых колебаний
сварочного инструмента и усилия нагружения инструмента. Данный способ сварки
как бы объединяет отдельные качества термокомпрессионной и УЗ-сварки,
обеспечивает высокое качество соединения при существенном смягчении режимов
сварки, прежде всего температуры. ТЗС используется в первую очередь при
автоматизированной сборке приборов, критичных к температурам свыше 200-250 °С.
Применим этот способ сварки и для сборки толстопленочных ГИС. Качественные,
устойчивые к повышенным температурам (150 °С) и термоциклированию (100
циклов; –55...+150 °С) соединения золотой проволоки с медными печатными
проводниками получаются ТЗС при температуре подложки 105-200 °С.
Практически ТЗС начинают широко применять и для сборки ИМС и БИС массовых серий
с целью смягчения режимов и снижения критичности сварочного процесса к
колебаниям качества соединяемых материалов.
Из
всех видов сварки, применяемых в производстве изделий микроэлектроники, ТЗС
является наиболее сложной в реализации, но отличается большой гибкостью в
выборе режимов, а поэтому весьма перспективна для автоматизированной сборки.
Использование при ТЗС ультразвуковой энергии наряду со снижением температуры
обусловило ряд преимуществ: увеличение скорости, относительная легкость
установления приемлемых режимов, улучшение свариваемости более широкой
номенклатуры материалов соединяемых поверхностей. Важным достоинством ТЗС по
сравнению с УЗС является меньшая критичность к жесткости конструктивных
элементов корпуса.
Термокомпрессионной
сваркой (ТКС) называют микросварку
давлением в твердой фазе элементов, нагреваемых от постороннего источника
теплоты, с локальной пластической деформацией в зоне сварки. Различают
термокомпрессионную микросварку с общим, импульсным, косвенным и
комбинированным нагревом.
Основными
параметрами режима термокомпрессии являются: усилие сжатия соединяемых
элементов F, температура нагрева инструмента Т, длительность
выдержки под давлением t.
Выбор
усилия сжатия F определяется допустимой деформацией присоединяемого
проводника, которая для золотой проволоки составляет 50-70 %, алюминиевой - 60-80
%. Температура нагрева не должна превышать температуру образования эвтектики
соединяемых материалов и находится в пределах 250-450 °С.
Длительность выдержки выбирается в зависимости от сочетаний свариваемых
материалов в диапазоне 1-10 для достижения максимальной прочности соединения.
Для
сварки применяют золотую проволоку диаметром 30 мкм, которую обезжиривают в
спирте и отжигают в течение 5 мин при температуре 600 °С. ТКС
проводится внахлест (клином) (рис. 4, а) или встык, с образованием
шарика (рис. 4, б). Шарик из золотой проволоки образуется в пламени
водородной горелки или электрическим разрядом. Диаметр шарика составляет 1,5-2
диаметра проволоки. Правильная форма шарика и отсутствие оксидов на его
поверхности улучшают качество соединений.
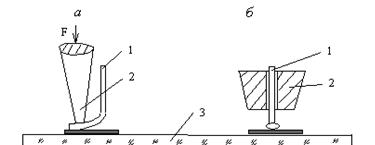
1 – проволока; 2 – инструмент; 3 – подложка
рис. 4. Схемы
термокомпрессионной сварки:
Для
ТКС рекомендуются рубиновые капилляры, имеющие более высокие износостойкость
рабочих поверхностей, коррозионную стойкость и чистоту поверхности. Обозначение
капилляра: КТ51-25-150-2-30 (КТ - капилляр для термокомпрессионной сварки, 25 -
диаметр проволоки, 150 - диаметр D, 30 - размер R). Наибольшая
прочность соединений достигается при использовании инструмента сложной формы: с
ребром жесткости или типа "рыбий глаз" (рис. 5).
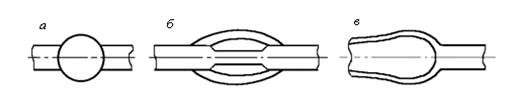
а - обычное; б - с ребрами жесткости; в - типа
“рыбий глаз”
рис. 5. Типы
термокомпрессионных соединений
После
сварки в процессе электротренировки возможно появление интерметаллидов AuxAly:
пурпурного AuAl2, затем рыжего, а через некоторое время фазы черного
цвета, имеющих низкую прочность и высокое электрическое сопротивление. Скорость
процесса разрушения соединения возрастает при повышении температуры. Расчеты
показывают, что при температуре 100 °С падение прочности вдвое
произойдет через 10 сут., а следующее падение прочности вдвое - через 7 лет.
Повышения
качества ТКС добиваются подачей в зону сварки осушенного защитного газа
(аргона, азота, формиргаза) и снижением температуры. Для ТКС используется
современное автоматическое оборудование (табл. 2).
Табл.
2 - Характеристика установок термокомпрессионной сварки
Параметры |
ЭМ-490
|
ЭМ-4030 |
ЭМ-4060 |
Hitachi (Япония) |
Диаметр вывода, мкм
|
20-60 |
20-60 |
20-60 |
20-60 |
Способ соединения |
Встык, внахлестку |
Внахлестку |
Встык, внахлестку |
Встык |
Температура нагрева, °С |
250-400 |
250-450 |
250-450 |
До 450 |
Контактное усилие, Н |
0,4-3 |
0,4-3 |
0,4-3 |
0,3-2,5 |
Время сварки, с |
0,05-0,3 |
0,4-3,6 |
0,04-0,3 |
0,05-4,0 |
Производительность, сварок/ч |
12 500 |
300 |
10 000 |
18 000 |
Преимущества ТКС заключаются в следующем: возможность сварки
прецизионных элементов с минимальной толщиной до 5 мкм, некритичность к
небольшим изменениям (±10 %)
параметров режима сварки, возможность групповой технологии контактирования. К
недостаткам следует отнести: небольшое число хорошо свариваемых материалов,
ограничение толщин свариваемых элементов до 0,13 мм, сильную зависимость
качества соединений от состояния свариваемых поверхностей, необходимость
подогрева деталей до 350-400 °С, увеличенное значение переходного сопротивления контактов,
возможность образования интерметаллидов, ухудшающих качество и надежность
соединения.
Сварка расщепленным (сдвоенным) электродом применяется в
технологии электрического монтажа, в частности при получении контактных
соединений планарных выводов ИМС и ЭРЭ с контактными площадками плат, плоских
ленточных проводов с выводами печатных разъемов и др. Метод пригоден для сварки
таких материалов, как медь, серебро, золото, алюминий, никель толщиной 0,03-0,5
мм. Подготовка свариваемых поверхностей заключается в предварительном отжиге
материалов для снятия внутренних напряжений и увеличения пластичности,
обезжиривании поверхностей химическими растворами. Сварка выполняется
электродом, изготовленным из вольфрама или молибдена в виде двух токопроводящих
частей, разделенных зазором h = 0,02-0,25 мм, либо с помощью
диэлектрической прокладки (рис. 6.).
Сварку осуществляют одним или несколькими импульсами
конденсаторного разряда с различной длительностью, мощностью и интервалами
между импульсами. Усилие прижима электродов при сварке 0,2-1,5 Н создается в
момент нагрева до максимальной температуры и снимается до окончания действия
импульса тока. При этом ИМС и ПП получают незначительную термическую нагрузку.
Сварку проводят на установках типа "Контакт-3А" (производительностью
250 сварок в час), ЭМ-425А, ЭМ-220, ЭМ-441 (800-2300 сварок в час) при
длительности сварочного импульса 0,02-0,8 с.
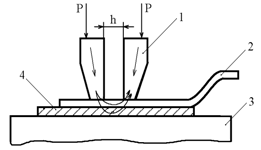
1 -
электроды; 2 - вывод
ИМС;3 - плата; 4
- контактная площадка
рис. 6. Схема сварки расщепленным электродом
К недостаткам рассмотренного способа относятся необходимость
никелирования плат и золочения выводов ИМС, точное позиционирование выводов,
трудность группового контактирования, более высокая стоимость по сравнению с
пайкой.
Лазерную микросварку использует для проводов в полиуретановой изоляции,
коваровых и никелевых выводов радиоэлементов с контактными площадками, плат,
проволочных выводов ИМС внахлестку, проволоки малых диаметров из золота, меди,
алюминия с напыленными на керамику, стекло, ситалл металлическими слоями и т.
п. Преимущества лазерного излучения:
·
высокая
локализация мощности в зоне нагрева (до 1000 МВт/м2);
·
безынерционность
воздействия, что позволяет вести нагрев импульсами малой длительности (1-10 мс)
и очень точно дозировать энергию излучения;
·
очень малая
зона термического влияния (0,03-0,25 мм) при минимальном диаметре пятна нагрева
0,01 мм;
·
не требуется
вакуум, работа может выполняться в атмосфере любого состава;
·
возможны
соединения материалов с существенными различиями оптических, теплофизических и
механических свойств;
·
легкость
автоматизации путем применения микропроцессоров и транспортных систем.
Источником лазерного излучения являются оптические квантовые
генераторы (ОКГ), которые по агрегатному состоянию рабочего вещества
подразделяются на газовые, жидкостные и твердотельные. В зависимости от
способов возбуждения рабочего вещества ОКГ работают с оптической либо
химической накачкой в непрерывном или импульсном режиме, а также в режиме
синхронизации модуляции.
ОКГ на неодимовом стекле и рубине имеют высокую удельную мощность
(до 10 000 МВт/м2), однако их применение ограниченно из-за низких
эффективности и частоты следования импульсов. ОКГ на алюмоиттриевом гранате (АИГ)
имеют рабочую длину волны 1,06 мкм и обеспечивают удельную мощность до 1000
МВт/м2 в сочетании с высокой частотой следования импульсов (до 20
Гц) благодаря низкому порогу накачки и хорошей теплопроводности рабочего
вещества. Газовый лазер на СО2 работает с еще большей эффективностью
как в непрерывном, так и в импульсном режиме, однако его излучение длиной волны
10,6 мкм хорошо отражается металлами.
Алюмоиттриевый гранат - монокристаллический материал, выращенный с
ориентацией по кристаллографической оси <100>. Он представляет собой
соединение Al2O3 и отличается очень высокой
теплопроводностью (0,13 Вт/(см·К)), малым коэффициентом теплового расширения
(6,96·10–6 К–1 ), высокой механической прочностью (175
МПа), а также малым порогом возбуждения. Для генерации излучения в состав АИГ
вводятся активизирующие ионы трехвалентного неодима - элемента из группы
лантанидов - в количестве 0,5-1 %.
Мощность лазерного излучения 125 Вт достигается благодаря
использованию двух активных элементов в излучателе. Коэффициент пропускания
выходного зеркала (до 20 %) является оптимальным и обеспечивает максимальную
мощность лазерного излучения при номинальной силе тока, проходящего через лампу
накачки. Активный элемент и лампа накачки размещаются в непосредственной
близости друг от друга и помещаются в отражатель, повышающий долю энергии
светового излучения лампы.
Основным элементом излучателя является квантрон, в состав которого
входят активный элемент, отражатель, корпус, штуцера охлаждения, фланцы и
втулки крепления. Отражатель представляет собой моноблок из легированного
европием кварцевого стекла в форме эллиптического цилиндра с полированной
боковой поверхностью, покрытой слоем серебра. На внешний слой моноблока
нанесено защитное покрытие из меди и никеля.
Кварцевое стекло отражателя с легирующими добавками не пропускает
вредное для активного элемента ультрафиолетовое излучение лампы накачки, что
позволяет использовать во внутреннем контуре системы охлаждения лазера
дистиллированную воду без каких-либо фильтрующих добавок и тем самым
значительно повышает эксплуатационные свойства лазера. Благодаря эллиптической
форме отражателя распределение энергии накачки по сечению активного элемента
имеет максимум в центральной части, что увеличивает эффективность генерации
излучения.
Активный элемент типа ГП 6,3х100 выполнен в виде круглого стержня
диаметром 6,3 мм и длиной 100 мм, изготовлен из монокристалла АИГ,
активированного трехвалентными ионами неодима. Резонатор излучателя образован
двумя зеркалами с многослойными диэлектрическими отражающими покрытиями. Основу
зеркал составляют подложки, имеющие вид шайб диаметром 40 мм, толщиной 4 мм,
изготовленные из стекла КУ-1. Выходное зеркало имеет коэффициент пропускания 20±2 %, а глухое - не менее 0,2 %.
Изменение положения поверхности зеркала относительно оси лазерного излучения
(юстировку) осуществляют путем поворота юстировочных винтов.
Система охлаждения лазера - жидкостная двухконтурная с
теплообменным устройством типа "вода-вода" и термостабилизацией охлаждающей
жидкости, циркулирующей по замкнутому контуру с помощью жидкостного насоса.
Наряду с хорошими теплофизическими характеристиками, доступностью и
безопасностью охлаждающая вода имеет высокие стабильные коэффициенты
пропускания излучения, оптической накачки и способностью отфильтровывать
инфракрасную часть спектра. Во внутреннем контуре используют только
дистиллированную воду.
Средняя мощность излучения в импульсе
,
где Е - энергия излучения; t - длительность
импульса.
При непрерывном излучении лазера длительность воздействия
,
где d - диаметр луча; v - скорость сканирования
платы относительно луча. Тогда средняя мощность излучения , а средняя плотность мощности излучения для луча
круглой формы .
Для оценки мощности лазерного излучения используют измеритель
средней мощности и энергии импульсов ОКГ ИМО-2, имеющий погрешность 10 %.
Промышленность выпускает ряд автоматов лазерной сварки и пайки с
программным управлением на базе лазера ЛТН-102А: для сварки - установки типа
"Квант-10", "Квант-12" с энергией излучения до 15 Дж и
частотой 60 импульсов в секунду, для пайки - ПЛП-2, "Квант-50",
"Квант-52" производительностью до 330 соединений в минуту и мощностью
излучения 125 Вт.
К недостаткам лазерного излучения как активирующего фактора при
пайке и сварке относятся: сложность технологического оборудования;
нестабильность лазерного излучения во времени; особые требования техники
безопасности; возможность термической деструкции диэлектрического основания
печатной платы из-за значительного поглощения лазерного излучения этими
материалами; большая энергоемкость, малый КПД ( около 1 %); повышенные
требования к точности изготовления плат; необходимость точного совмещения платы
с фокальной плоскостью лазера.
При монтажной микросварке не допускаются следующие дефекты: обрыв
проволочного вывода и пересечение выводов; утончение вывода более 1/4 диаметра;
расстояние между привариваемыми проволоками меньше трех диаметров проволоки;
высота петли более 0,3 мм над уровнем кристалла; сильное натяжение, изгиб
проволочного провода, приводящий к соприкосновению его с кристаллом; длина
свободных концов проволоки более одного диаметра в соединении с контактными
площадками кристалла и более трех диаметров - с траверсами; смещение сварных
соединений за пределы контура траверсы.
Литература
1. Технология поверхностного монтажа:
Учеб. пособие / Кундас С.П., Достанко А.П., Ануфриев Л.П. и др. – Мн.: «Армита
- Маркетинг, Менеджмент», 2000.
2. Технология радиоэлектронных
устройств и автоматизация производства: Учебник/ А.П. Достанко, В.Л.Ланин, А.А.
Хмыль, Л.П. Ануфриев; Под общ. ред. А.П. Достанко. – Мн.: Выш. шк., 2002
3. Гуськов Г.Я., Блинов Г.А., Газаров
А.А. Монтаж микроэлектронной аппаратуры М.:Радио и связь, 2006.-176с.
|